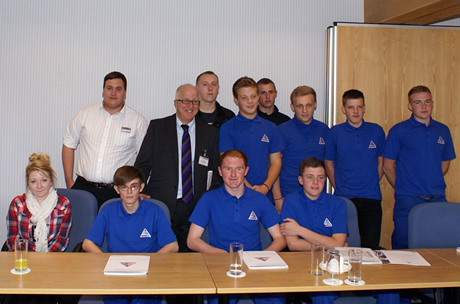
An MP for an industrial constituency has called for apprenticeship programmes to be set up across the UK.
“Don’t write off British manufacturing and British engineering, but we do need more apprentices,” said Rotherham MP Denis MacShane.
He was launching the £1.25m programme created by mechanical seal manufacturer AESSEAL plc, the world’s fourth-largest in its field, with its Global Technology Centre in Rotherham.
The company, which employs some 1,500 worldwide, including 300 in Rotherham, is ploughing its own money into the five-year programme. At least 30 apprentices will be taken on over that period. And on the basis of past performance, including 29 consecutive years’ sales and profit growth, the company believes that the numbers and investment could grow.
“I want to see more examples of this around the UK,” Denis MacShane said, arguing that it would make Britain a stronger economy and help tackle youth unemployment. “In Germany, a quarter of all employees are in apprenticeship schemes. It means quality is better right across their economy, and that is one reason Germany is more competitive.”
AESSEAL sees the programme as creating “the engineers of the future”. Group managing director Chris Rea said it was important to the future of the company. Production and personnel director Richard Cook, a former apprentice himself, shaped the training and is implementing it with local organisation Brinsworth Academy of Engineering.
“This is a significant investment for the company and for the region. We need well-trained young people in manufacturing,” he said. “It’s a local and regional problem, but also a national and even international one. But unless we tackle it our European neighbours could steal away the high-value end of manufacturing that’s so important to this country.”
Before the launch, he warned: “If the UK is to compete credibly in manufacturing, it needs to re-evaluate the term ‘engineer’, giving it the esteem it has in other leading manufacturing nations, such as Germany and Japan.
“We must also stop devaluing ‘apprenticeships’ recognise them as a three to five year programme of skills acquisition to create competent machinists – quite aside from the development necessary to go into production supervision and management.”
As testament to their commitment to apprenticeships, AESSEAL has differentiated its initiative by developing a two year off-the-job programme, fully accepting that there will be no measurable productive return from the apprentices during this period.
Richard Cook condemned current notions that good apprenticeships can be delivered by a 42-week programme: “People are deluded if they think the creation of an engineer can be compressed to this extent. Some of our past apprentices from such schemes were unable to demonstrate even the most basic of machining skills.
“We have a huge problem with skills in manufacturing, locally and nationally. We also suffer from cynicism about manufacturing being a dying sector. It’s not. This country – commentators, politicians and others – should recognise that, and put much more than words into promoting and encouraging it.”
He is an advocate of apprenticeships for a reason: “I have a passion for apprenticeships, because I am an apprentice-trained engineer.”
Rotherham Metropolitan Borough Council’s Cabinet Member for Regeneration, Cllr Gerald Smith, said the initiative was “the sort of bold, confident move that the local and national economies need”. He backed Richard Cook’s call for proper respect for the term “engineer”.
AESSEAL’s commitment to quality training was recognised at the launch by the Institution of Mechanical Engineering. IMechE business development manager Denis Healy presented the company with a certificate marking its incorporation into the IMechE Accredited Apprentice Scheme.
Several young apprentices were part of the launch, and one, Aaron Stephenson, told the audience of the opportunities AESSEAL offered him and others like him.
Richard Cook said:
It’s about opportunities for personal development, about giving people experience, career prospects and a salary, all at the same time – earn as you learn! We need truly great people, be they talented machinists or those with aspirations towards higher education – up to and including PhD level.
“There are very few people experienced enough to manufacture one-off components on complex multi-tasking machinery with no room for error. One tiny mistake and thousands of pounds’ worth of raw material can be scrapped, delaying delivery and letting down the customer. Everybody in our company is expected to go the extra mile to ensure this never happens.”
He is scathing about training provision in general. “Some organisations are drawing down millions in EU funds and not meriting it. But we use a local company, Brinsworth Academy of Engineering, because they demonstrated a genuine will to work with us to improve local apprenticeship provision. In return we directly support Brinsworth’s Strategic Advisory Board.”
AESSEAL believes that competition for experienced engineers means it must grow its own.
“That means we can also instil in them AESSEAL’s core values,” said Richard Cook. “Especially the all-encompassing ethos of giving customers such exceptional service, from product quality to after-care, that they need never look for an alternative source of supply.”
The company knows that investment in well-trained employees gives lucrative payback over time through increased efficiency and innovation. But it also insists on a clear, legally-binding agreement those undertaking higher education are expected to sign – anyone leaving before or within a few years of qualifying must repay a reducing proportion of course fees, immediately on leaving.
“Yes, it does focus the mind,” admitted Richard Cook. “But we hope the people will stay with us for years as great machine operators, sales people, administrators – whatever they develop into, because they have stimulating and challenging career paths.
“We have one young person on our Advanced Apprenticeship Programme with the specific remit of becoming a sales engineer. Another rejected a university place to join us as an apprentice and is now being fast-tracked through our Management Development Programme. One of our female apprentices has just made the transition from manufacturing workshop to sales administration, creating vital packages that will persuade companies to choose our products and services.”
AESSEAL’s advanced technology, people development and process control have attracted some of the UK’s largest and most advanced companies to benchmark their processes against those of the Rotherham company.