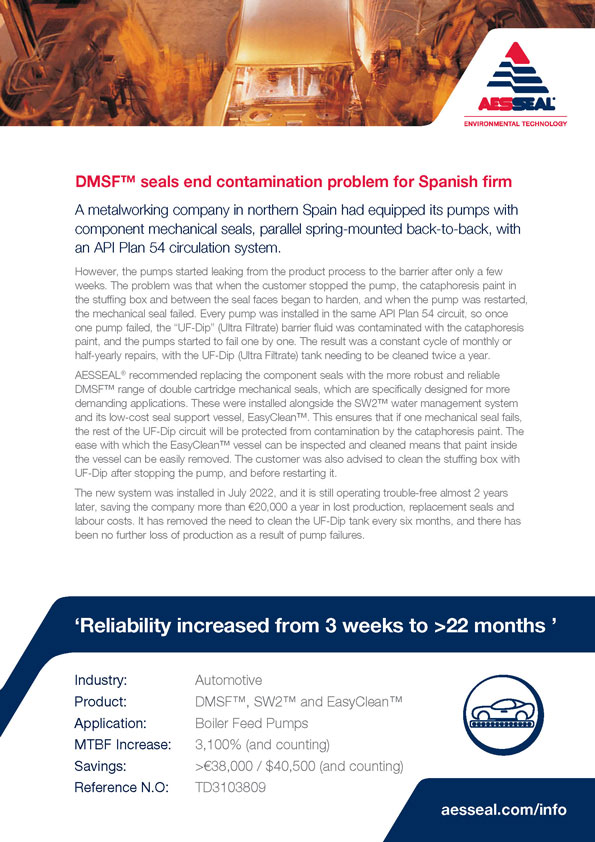
A metalworking company in northern Spain had equipped its pumps with component mechanical seals, parallel spring-mounted back-to-back, with an API Plan 54 circulation system.
More Industry Related Content
More API Related Content
By Álvaro Masero
What product or service does this company provide for the automotive industry?
This is a company based in northern Spain which makes car body parts using a process called cataphoresis. Cataphoresis is a way of electro coating metals to increase their resistance to corrosion. It is the standard way of providing auto parts with the best possible protection against rust.
How did the contact between AESSEAL and the company come about?
The customer had been buying OEM component seals for many years. The customer had reliability issues because the component seals didn’t work properly in this application, but they didn’t know that there was an alternative, so they continued buying the same component seals. I knew that this customer had a cataphoresis process so I visited them to see the application and I explained to them that they could improve the reliability with another solution.
What was the problem?
The mechanical seals they were using were not fit for purpose. Every time they stopped a pump, the cataphoresis paint would harden. When they restarted the pump, the seal would fail. This meant that the pumps had to be stopped to put in new seals, bringing production to a standstill. It was very frustrating, and it was costing the company a lot of money in labor costs and in lost production.
Why did they decide to do business with AESSEAL?
I prepared a presentation to show them our successful experience in the sealing of the cataphoresis pumps. I convinced them that they could solve the problem by replacing the component seals with the more reliable DMSF™ double cartridge mechanical seals, which are designed for more demanding applications, and by adding our auxiliary system EasyClean™ SW2. The EasyClean™ SW2 system is very effective because if one mechanical seal fails, the system keeps the rest of the "UF-Dip" (Ultra Filtrate) circuit protected from the cataphoresis paint. So far there hasn’t been any mechanical seal failure, but the day that one pump fails the rest will be protected. In addition, the paint inside the EasyClean™ SW2 vessel can be removed very easily.
How did you convince them that the DMSF™ range was the answer to their problems?
I showed them the excellent performance of the DMSF™ seal and its special features such as the self-aligning stationary seal faces and the unique bi-directional pumping ring to dissipate heat from the seal faces.
Did it take long for them to see the benefits?
The first pump to be fitted with this system was still working a month later and the customer realized that their reliability problems had been resolved. They then decided to purchase the same system for another three pumps.
Were there any problems during installation of the new system? If so, how did AESSEAL overcome them?
It was the first time that the customer had assembled this type of mechanical seal, so to ensure that everything went perfectly, I offered to supervise and guide them in the installation of the seal and seal support systems to give them confidence.
What are the unique selling points which distinguish AESSEAL from its competitors?
We offer a high-quality product, a high level of technical support, and we are close to our customers. We are always there for them when they need us and never leave them behind. Our service is perfect!
Does AESSEAL offer a regular inspection or maintenance service to this customer to make sure that the seals are in good condition and working well?
Since then, I have established a good relationship with the customer, and sometimes I call him to check that everything is OK. Once a year I visit the site to check that the installation is still working properly.
Since the installation, is the customer satisfied with the product? How has it solved the problem of leakage?
The customer is very satisfied with our product and with our after-sales service, and has asked us to supply mechanical seals for pumps in other factory applications such as the “pre-clean” stage or “phosphate dipping”.