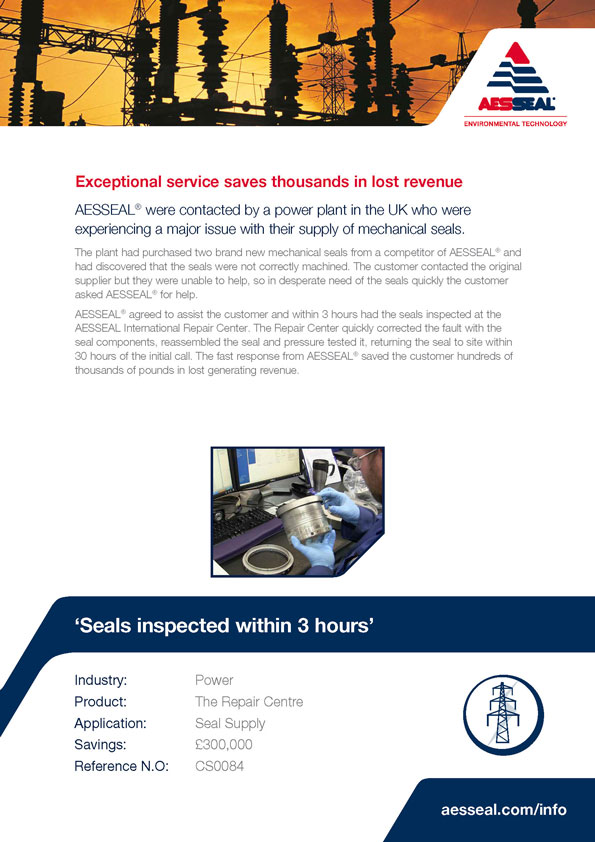
AESSEAL were contacted by a power plant in the UK who were experiencing a major issue with their supply of mechanical seals.
More Industry Related Content
By Oliver Crank
How did the initial contact come about?
This was an existing customer that we had started working with just 12 months previously. We had done some very good work for them onsite including HP feed pump mechanical seal upgrades, so they were aware of the quality of service we provide.
The case study says the competitor’s seals were not correctly machined. What problems did it cause?
The machining mistake meant the seal would not fit on the shaft. It was a clear error on the part of the supplier. We measured the sleeve, which confirmed that the size was incorrect. To rectify the problem we proposed machining out the seal sleeves to the correct size. Because of the level of trust we had built up from the work we had already done for them, they immediately agreed to our recommendations.
Did this solve the problem?
Yes. The seal was now the correct size, which meant the site could operate normally. It was a very efficient operation. Once we had been contacted, we had the seals inspected at the AESSEAL International Repair Center within a few hours. The Repair Center was able to correct the fault, reassemble the seal, pressure test it, and return it to the site within 30 hours of the initial call. The speed of the response from AESSEAL® saved the customer hundreds of thousands of pounds in lost generating revenue.
Were there any unexpected challenges?
No. The whole operation went very smoothly. Being able to solve the problem so quickly meant that there was no interruption to the company’s operations, which saved them a large amount of money. The seals are still working effectively, and the customer is very satisfied with the results.
Do you keep in contact with the company to monitor the performance of the seals?
Yes. I visit the site on a regular basis to make sure that everything is working properly. The work we carried out and the quality of service we were able to provide led to AESSEAL® being named the preferred supplier of mechanical seals on the site. We have since installed many other seals onsite including a double seal upgrade on the main cooling water pumps.