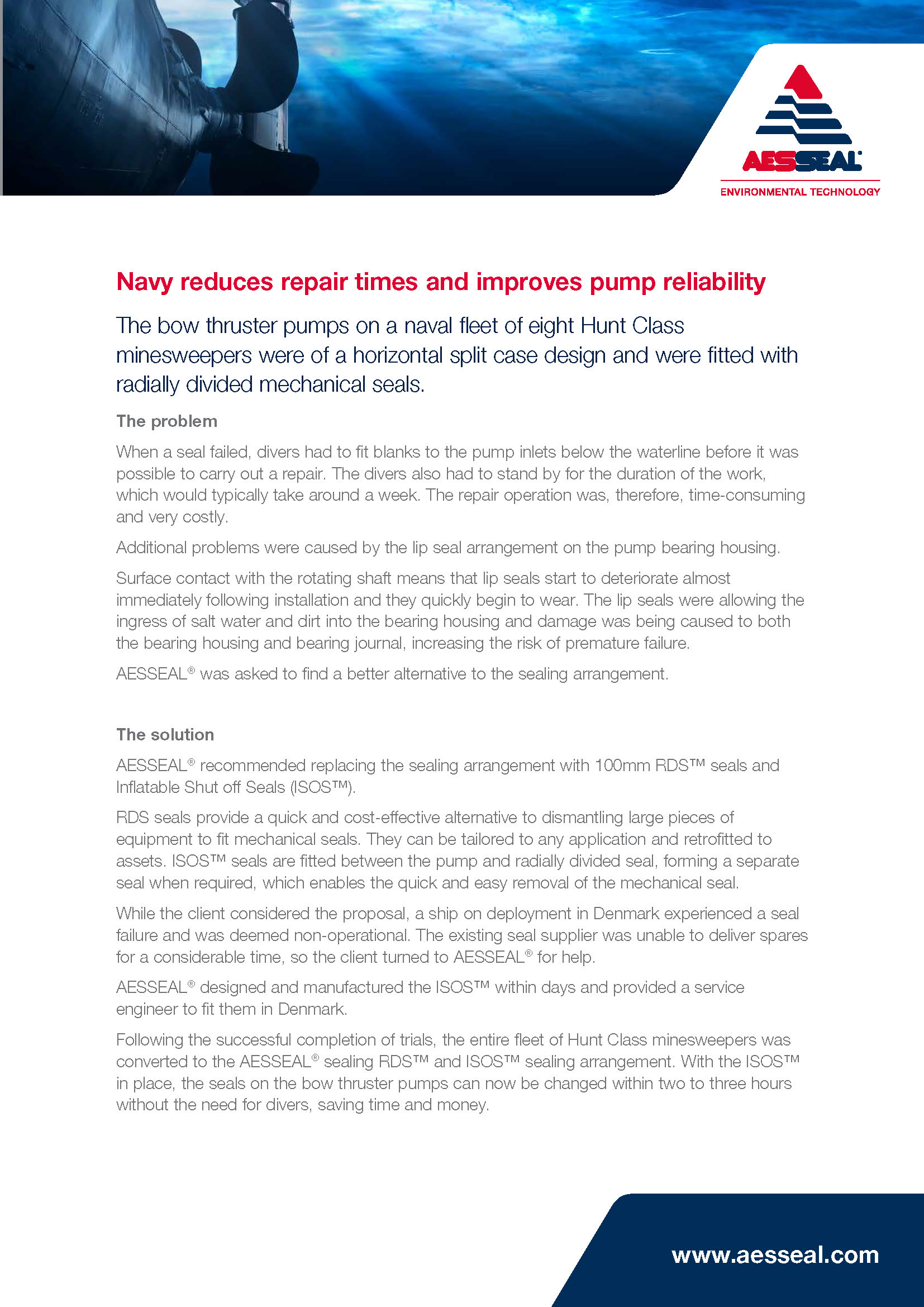
When a seal failed, divers had to fit blanks to the pump inlets below the waterline before it was possible to carry out a repair. The divers also had to stand by for the duration of the work, which would typically take around a week. The repair operation was, therefore, time-consuming and very costly.
More Industry Related Content
By Simon Spiller
What exactly is a bow thruster, and why were they causing problems?
A bow thruster is simply a way of helping to manoeuvre a vessel at low speed. Vessels are also fitted with stern thrusters, which carry out basically the same function. The bow thruster pumps on the Navy minesweepers were of a horizontal split case design, fitted with conventional cartridge seals. These could not be split, which meant that the bearings had to be removed every time the seals were changed. The use of conventional seals, combined with the fact that the pump was used as a bow thruster, meant that if a seal failed, it allowed seawater to enter the vessel.
The Navy was unhappy with the situation. Why was that?
They were not happy about the time it took to carry out repairs in the event of a seal failure. Some of the work had to be done below the waterline, which meant that they had to get divers in and then keep them on standby while the repair was being carried out. This generally took the best part of a week, during which time the ship was out of action. All in all, a time-consuming and expensive business.
How did AESSEAL® get involved?
They asked us if we could come up with a better option. Of course we said we could. We recommended replacing the existing seals with our own radially divided RDSXTM seals. The great advantage of these seals is that they are radially split. You don’t have to spend a lot of time removing or stripping equipment, and the entire process can be carried out in the matter of a few hours rather than taking several days. We also supplied them with ISOSTM seals (Inflatable Shut-Off Seals). These are fitted between the pump and the faulty mechanical seal. They remove the need to employ divers to blank the hull inlets, making it a lot easier and quicker to remove the old seal in order to replace it with the new one.
Was it easy to convince the Navy to adopt the AESSEAL® solution?
They didn’t say yes immediately, but then as luck would have it, while they were thinking about our proposal they had a problem with a seal failure on one of their minesweepers on duty in Denmark, and they had to take it out of service. Their existing seal supplier told them spares weren’t immediately available, which gave us the chance to show them how quickly we could react. We were able to design and manufacture the ISOSTM within a few days and to send it with one of our engineers to Denmark, where he supervised the fitting of both this and the RDSXTM.
Were they happy with the outcome?
Absolutely. With the ISOSTM in place and using AES radially split seals, it means that they can now be changed within two to three hours without the need for divers, which means big savings in time and money. In fact they were so pleased with the service they received and with how quickly we were able to complete the repair that they’ve since converted their entire fleet of Hunt Class minesweepers to the AESSEAL® RDSXTM and ISOSTM sealing arrangement.