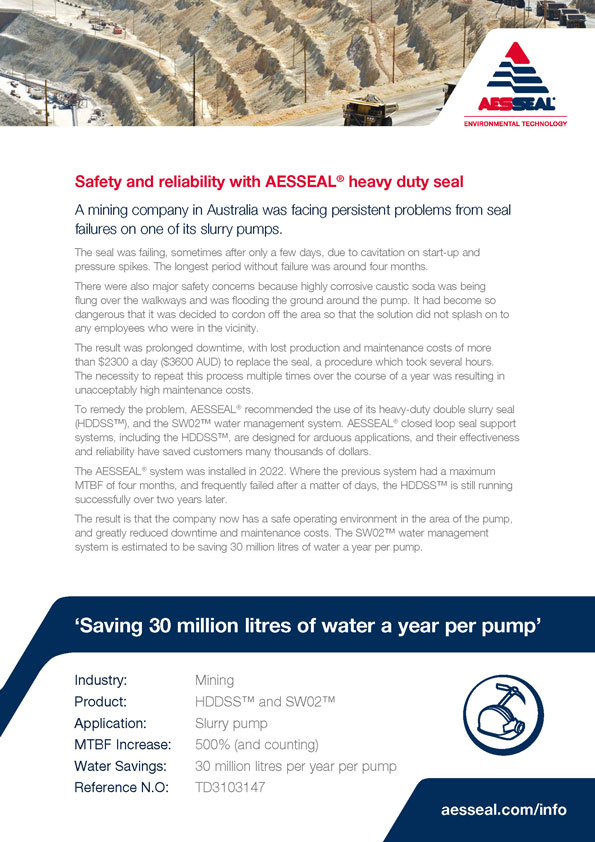
A mining company in Australia was facing persistent problems from seal failures on one of its slurry pumps.
More Industry Related Content
By Peter Garnett
How did AESSEAL® get involved? Was this an existing customer?
This company was not an existing customer. We got involved after we were contacted by one of their engineers, who turned out to be someone we had dealt with previously when he worked for another company. He called me to ask if we could help out with a problem pump at his new company.
What was the problem with the existing seal?
The company was using a competitor’s double seal on one of its slurry pumps, but the seal was failing, sometimes after only a few days, due to cavitation on start-up and pressure spikes. The cavitation was caused by the inconsistent fluid level inside the vessel they were pumping from. The reason for the pressure spikes was unknown, but they were probably caused by partial blockages in the discharge. The result was that the pump was failing on a regular basis, sometimes after only a few days. The longest period without failure was around four months.
Were there also some concerns over safety?
Yes. When the pump failed, highly corrosive caustic soda was ending up on the walkways and was flooding the area around the pump. In fact, it had become so dangerous that the company had to put a cordon in the immediate vicinity of the pump so that the solution didn’t splash on to any employees who were working nearby.
What did you suggest as a possible solution to the problem?
We recommended the use of the AESSEAL® heavy-duty double slurry seal (HDDSS), and the SW02 water management system. The HDDSS seals are specially designed for difficult applications, and because they’re so tough and reliable, they save customers thousands of dollars in downtime and repair and maintenance costs. That was the case here. Another advantage of the HDDSS was that it was very easy to retrofit and install on site, and because it’s a double seal it will handle some cavitation.
Was it difficult to convince the company to change?
Yes. This is a hard company to contact and no matter how bad the problem is they are very reluctant to change their existing suppliers. Every time a seal failed, it was costing them more than $2300 a day in lost production because replacing the seal took several hours, and they were having to do this several times a year. Even so, the only way we were able to persuade them to try our seal was to offer a six-month trial at no cost until they were happy. Once the seal proved itself, they paid for it.
Were there any particular challenges with this installation?
No. Because the HDDSS has the pump sleeve and the stuffing box built into the seal, it requires no modification to the pump. There is no need for a seal adaptor plate and pump sleeve.
Do you still monitor the performance of the seal?
Yes, but only remotely through a third party. Since the start of COVID no suppliers are allowed onsite, only contract workers.
Do you have any updates about the performance of the seal?
The HDDSS seals run for between 24 and 28 months, compared with a maximum of four months when they were using the competitor’s seal. At the end of this period the pump is removed and sent to the OEM for repair; the seal is sent to AESSEAL® for repair and then returned to the OEM. The much longer seal life has resulted in greatly reduced downtime and maintenance costs, and a much safer operating environment. In addition, the SW02 water management system is estimated to be saving 30 million litres of water a year per pump.