How can seals pass the API 682 air test, and then leak upon installation?
Following a visit to a US refinery, we were asked to explain how seals supplied by a reputable manufacturer (an AESSEAL competitor) which had passed the API air test, could then leak upon installation.
They were understandably frustrated with their supplier – so they asked AESSEAL to help explain how this could happen.
API 682 and ISO 20149 is the premier standard for mechanical seals used on hazardous, flammable or toxic applications. The standard states the following objective:
An average liquid leakage rate of less than 5.6 g/h per pair of seal faces. (API 682 / ISO 20149, Section 10.3.1.4.1)
Additionally, each assembled seal must be subjected to a quality-assurance test. This involves connecting the complete seal to a tank of pressurised air, then measuring the pressure drop over five minutes to assess the leakage.
How could mechanical seals pass the air test, yet still leak upon installation?
We think we have an answer.
AESSEAL believe that the API-682 “air test” does not reflect best practice and could be vastly improved. We’ve been campaigning to have this changed, and we voluntarily submit our mechanical seals to a far stricter test.
To prove that the current test does not reflect best practice, we manufactured a sealing assembly which was able to pass the air test despite actually leaking 270 to 1,300 times the 5.6 grams (0.2 US fluid ounces) per hour maximum.
It goes without saying that with hazardous, flammable or corrosive products (the areas where API-682 is most often applied) a seal which can leak up to 1,300 times the intended maximum may represent a very real safety risk!
Watch the API 682 Air Test Video Below
This video documents the testing process and the results. This video contains audio description.
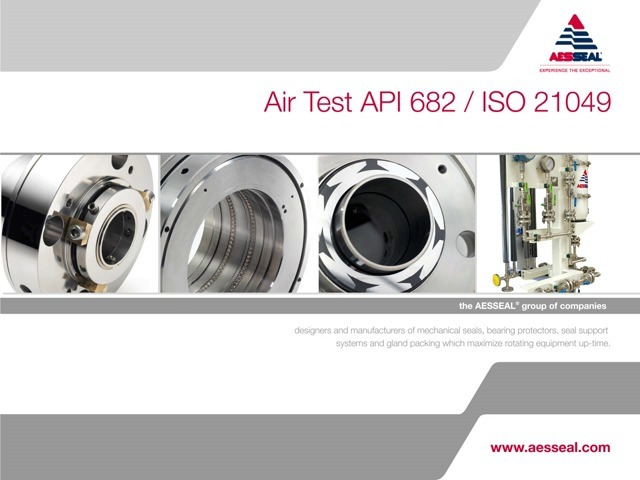
More Industry Related Content